Stripping machine for nickel screen
Nickel screen stripping machines has changed the entire production system and cost composition of the textile printing and dyeing industry. We have changed the environmental protection, efficiency, and quality issues of mechanical stripping from traditional chemical washing to laser stripping. To; Nowadays, high-pressure water stripping has become the mainstream cleaning method for rotary nickel mesh. Because it is more environmentally friendly and economical. Then the mechanical complexity of high-pressure water washing requires higher requirements. In order to make the mechanical operation more stable and efficient. We have crossed two generations of high-pressure water washing technology. Developed the latest third-generation direct water stripping machine. Let our customers lead the revolution in fabric printing.
Three style for stripping screen
The cleaning of three style
Customer will find the water stripping is more environmental and cleaner for stripping, first of all ,Quality is most important
for printing.so water striping style is our choice . but pls see follows comparison of laser and hyddraulic oil water strippig machine. hyddraulic oil water technical is more effective and cleaner than laser, but it need more power.and total cost for
every screen is expensive althrough quality is very good. another problem is hyddraulic oil push system is not stable and easy be controled by software. so we will keep researching for technical details and solve problem on it. at last, we develop
a new water stripping machine which is a direct way generator.that solve all problem of hyddraulic oil skill for high pressure
water. it stable and more effective. we will instroduce later.
Detailed parameter comparison of laser and water stripping
Three generation of water stripping machine
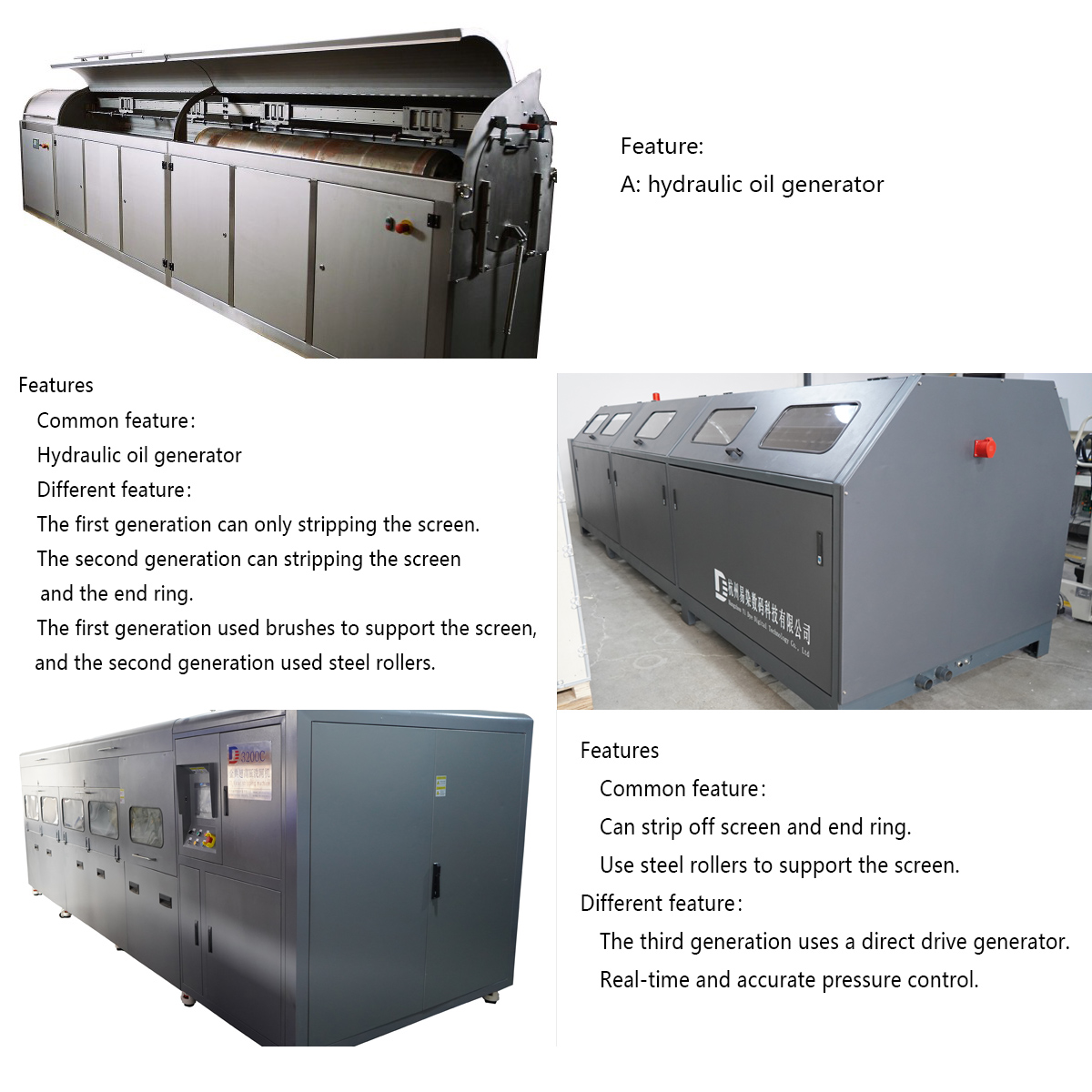
Comparison of generator for direct and hydraulic oil
In a printing and dyeing factory, there are 30,000 used screens in stock and 10,000 used per year.Assuming that only 60% of the used screens can be used, that is 18,000 screens. Now the price of 640, 2 meters, 125 mesh screens is around US$40. This means that you can save US$720,000. if you use our direct water stripping machine.
The 18,000 screens after stripping can be stripping again after use, usually one screen can be used 5 to 6 times. And as the workers are skilled, the reuse rate will be higher and higher. At present, the general recycling rate of Chinese printing and dyeing factories is above 80%.
According to existing experience, the water stripper will not cause damage to the screen. Only the screen making, transfer, printing, and washing process will cause damage to the screen.
Urgent orders and large orders can produce two or more sets of screens without being restricted by the cost of the screen. If the screen on the printing machine is damaged, it can be replaced at any time, so there is no need to stop the printing machine due to waiting for the screen to be remade.that will improve rate of working time and save cost of labour.